RFIDを活用した工程管理と在庫管理の革新
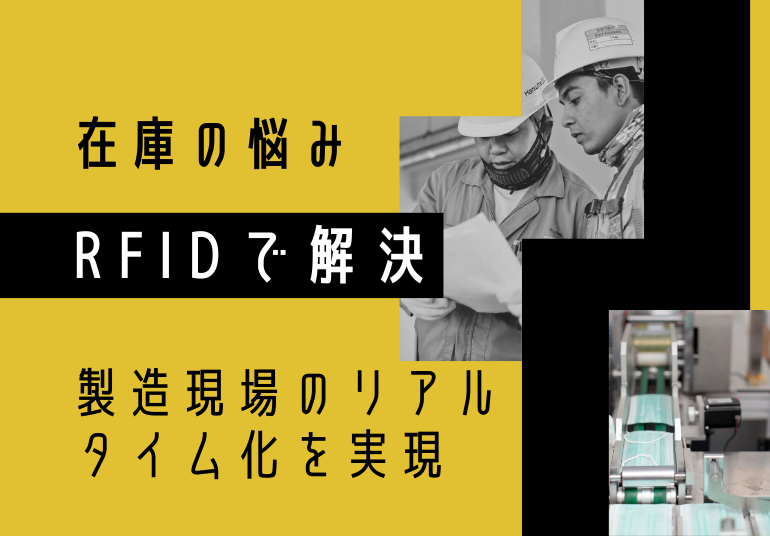
はじめに
製造業における効率化と精度向上が求められる中、RFID(無線周波数識別)技術が注目を集めています。今回は、私たちがサポートしたお客様の工場でのRFID導入事例を通じて、工程管理と在庫管理の改善についてご紹介いたします。
導入背景
お客様の工場では、従来のバーコードシステムを使用して在庫管理を行っていましたが、以下のような課題がありました。
-
- 在庫の不正確さ
手動での在庫管理により、誤差が生じることが多く、在庫状況の把握が困難でした。
-
- リアルタイムデータの不足
工程の進捗状況を把握するのが難しく、迅速な意思決定ができない状況でした。
-
- 誤出荷のリスク
出荷予定データと実際の在庫の照合が手動で行われていたため、誤出荷のリスクが高まりました。
これらの課題を解決するために、RFID技術の導入を提案いたしました。
導入プロセス
- ニーズの分析
まず、お客様の現状の工程管理と在庫管理のプロセスを詳細に分析し、RFID導入の目的を明確にしました。
- システムの選定
RFIDタグ、リーダー、ソフトウェアを選定し、お客様のニーズに最適なシステムを構築しました。
- 実装とテスト
RFIDシステムを導入し、実際のライン作業でテストを行いました。初期の段階では、従業員へのトレーニングも実施しました。
成果
工程管理の改善
-
- リアルタイム追跡
各工程の進捗状況をリアルタイムで把握できるようになり、ボトルネックの特定が容易になりました。
-
- データの可視化
工程の進捗を可視化することで、迅速な意思決定が可能になりました。
在庫管理の向上
-
- 在庫精度の向上
RFIDによる自動在庫管理により、在庫の正確性が向上し、欠品や過剰在庫のリスクが減少しました。
-
- 効率的な在庫確認
バーコードシステムと併用することで、在庫確認の精度が向上し、業務の効率化が図られました。
-
- 誤出荷の防止
出荷予定データをRFIDと照合することで、実際の在庫と出荷予定の一致を確認し、誤出荷のリスクを大幅に低減しました。
課題と対策
導入後、いくつかの課題も浮上しました。例えば、初期投資のコストやシステムのメンテナンスに関する問題です。これらに対しては、ROI(投資対効果)を定期的に評価し、必要に応じて改善策を講じています。
まとめ
RFIDを用いた工程管理と在庫管理の導入は、お客様の工場において大きな成果をもたらしました。今後もこの技術を活用し、さらなる効率化と品質向上を目指していきます。RFID技術の導入を検討している企業にとって、私たちの経験が参考になれば幸いです。